The Role of Wire Wound Resistor in Modern Electrical Engineering
Throughout modern electronics, wire wound resistors act as central elements. The complex operations and broad-range applications they offer strengthen numerous electronic devices. From straightforward projects to elaborate setups, its place remains unquestionable.
Understanding the Basics of Wire Wound Resistor
In their basic form, the wire wound resistor consist of a metal wire wrapped around a core. The wire is often made from alloys like Nichrome or Cupronickel, selected due to stellar conductive characteristics and heat endurance. This setup enables these structures to exhibit excellent performance across diverse circumstances.
The choice of core material is equally crucial, with common choices including ceramic, due to its insulating properties. Each core holds the winding securely, mitigating electrical interference and maintaining longevity. Prioritizing exactitude and execution, these resistors continue to serve various uses needing uniform quality.
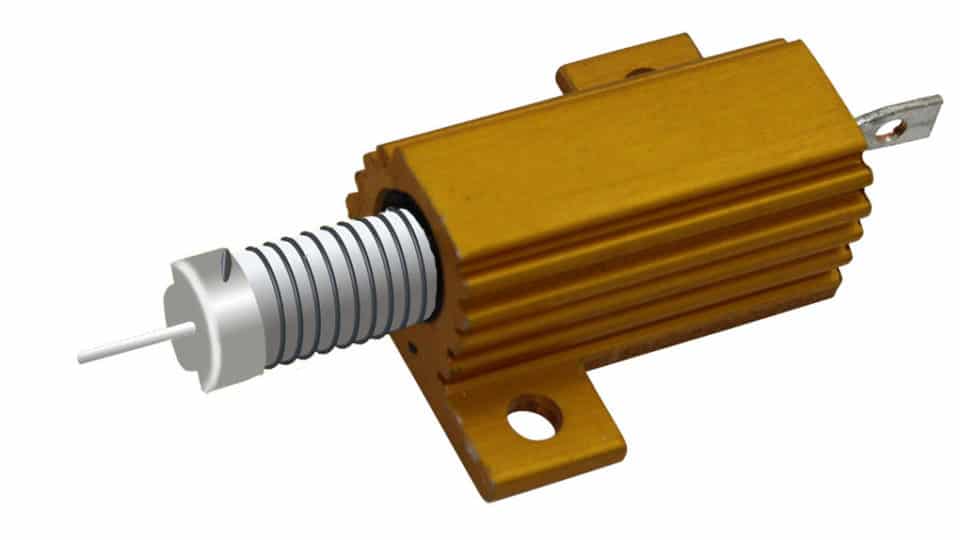
Versatile Use Cases for Wire Wound Resistor
The applications for wire wound resistors are vast, ranging from heavy-duty machines to consumer electronics, also tackling specialized industries. In sound engineering, they control audio fidelity, providing listener-friendly tunes. Recording studios utilize such resistors for consistent audio outputs.
Power handling frameworks incorporate wire wound resistor s due to their adeptness in handling heat. These resistors' thermal management capabilities make them the perfect choice for such systems. They uphold consistency, keeping systems cool, especially as power intensities vary.
Innovation in Wire Wound Resistor Materials
Recent technological strides in the world of resistors have boosted functional capabilities. New-age material formulations introduce advanced wires to circuit designs, offering better conductivity and enhanced heat control.
Design methodologies have also evolved to optimize spatial footprint. As technology shrinks, engineers focus on creating smaller yet powerful resistors. Additionally, integrating digital adjustments gives rise to intelligent component designs. Adaptive resistance values render them versatile for real-time adjustments, resulting in the optimized performance.
Factors to Consider in Wire Wound Resistor Design
Even though they hold many advantages, incorporating these resistors has its own set of limitations. The inductive nature, due to winding, usually causes complications in high-frequency applications, where unwanted frequency responses are introduced.
Further, layering ceramic cores demands attention to mechanical robustness, especially in dynamic environments, where physical exposure is heightened. Thermal-unstable scenarios add another layer of complexity because escalated heat levels could affect longevity.
The Horizon for Wire Wound Resistor Developments
As we look forward, there shines ample opportunity for advancing resistors to new height. The field continues to broaden, driven by future technological necessities. The continued march towards smaller footprints and finer measurement aspirations keep influencing the evolution.
The potential combination with IoT applications unlocks extensive opportunities, aligning with automated controls and monitoring. International tech requirements combined with enhanced material science marks the beginning of innovative resistor chapters, ensuring that wire wound resistors will continue defending their relevance for generations to come.